Collaborative initiative enhances resilient silicon carbide circuits capable of functioning at unprecedented high temperatures
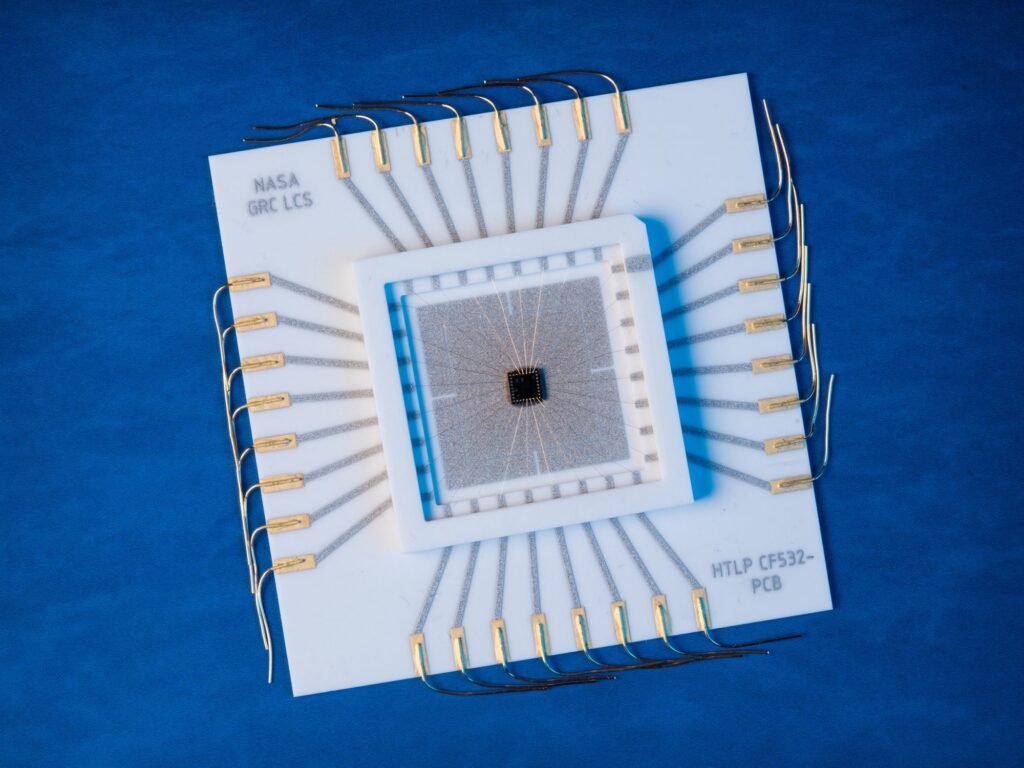
High-temperature resistant sensing and computing chips constructed from silicon carbide may propel advancements in aviation, electric and fossil-fuel vehicles, renewable energy, military applications, and space exploration—and researchers from the University of Michigan are spearheading a multimillion-dollar collaborative initiative to bring more of these technologies to the market.
Supported by the Silicon Crossroads Microelectronics Commons Hub, the initiative is commencing with an initial funding of $2.4 million, potentially scaling up to $7.5 million over a three-year duration.
Experts at NASA’s Glenn Research Center have been investigating the potential of silicon carbide, or SiC, as a high-capacity semiconductor for many years. SiC components can endure higher voltages, temperatures, and radiation levels compared to silicon alone. With a view toward studying the surface of Venus, they developed a SiC circuit capable of withstanding 930°F (500°C) for extended periods. NASA Glenn has also demonstrated a packaged device functioning over a thermal range of 1,800°F (1,000°C), from -310°F (-190°C) to 1,490°F (812°C), which is pertinent for aerospace applications.
SiC holds promise far beyond space endeavors—it is being increasingly utilized in power electronics for electric vehicles as well as solar and wind energy systems. Nevertheless, these applications have yet to fully leverage its durability under extreme conditions.
The newly initiated project aims to upscale NASA’s technology and fabrication methods to modern wafer dimensions while democratizing SiC chip design. Collaborators alongside NASA include GE Aerospace Research located in Niskayuna, New York; Ozark Integrated Circuits (Ozark IC), a tech firm in Fayetteville, Arkansas; and Wolfspeed, a semiconductor manufacturer based in North Carolina.
Although the technology has the potential to be applicable across various industries, this project will concentrate on aerospace, including electronic systems and sensors that enhance the reliability of aircraft engines and optimize their size, weight, and energy consumption. A significant aim is to showcase a packaged actuator for aerospace or engine applications. Actuators convert electrical signals into mechanical movement and are crucial components of control systems.
Collaborating with the industry and governmental bodies

“NASA, GE Aerospace, and Ozark IC have excelled in evolving this technology, which significantly impacts numerous applications. This project will establish a crucial pathway to advance and commercialize that technology,” stated principal investigator Becky Peterson, associate professor of electrical and computer engineering and director of the U-M Lurie Nanofabrication Facility.
“There is a need for advanced semiconductors produced domestically that can function in these demanding high-temperature environments.”
In this endeavor, NASA Glenn and GE Aerospace will collaborate to scale the fabrication process of the high-temperature SiC junction field effect transistor, or JFET, from 100 to 150-millimeter wafers.
“SiC-based high-temperature electronics will be fundamental in providing new capabilities for sensors and actuators that enhance the functionality of future Department of Defense engine platforms. Beyond jet engines, the capability to endure more extreme temperature ranges could unlock exciting novel applications in control and sensing for hypersonic technologies,” expressed Aaron Knobloch, platform leader for controls and electrical systems at GE Aerospace Research.
Ozark IC, which has partnered with NASA Glenn through the NASA Small Business Innovation Research program and licensing offices over many years, will provide support in packaging, integration, and process commercialization. Ozark IC has demonstrated a pathway for the technology to operate at over 1,400°F (800°C) integrated with advanced packaging.
This initiative builds upon Ozark IC’s existing work with the Department of Defense, where DARPA has facilitated the transition of SiC JFET-R technology to GE Aerospace’s 100 mm facility in New York, as well as its application for aerospace sensing through the DARPA High Operational Temperature Sensors (HOTS) program.
Wolfspeed, a pioneer and leader in SiC wafer manufacturing, will supply the specialized SiC wafers essential for these devices, leveraging its extensive expertise and capabilities in SiC epitaxy. Wolfspeed and the U.S. Department of Commerce are in the process of finalizing a proposed $750 million direct funding package to bolster the expansion of Wolfspeed’s silicon carbide production in North Carolina and New York. Additionally, Wolfspeed will collaborate with the team on design for commercialization.
“Ozark IC has been collaborating with NASA and GE Aerospace in bringing SiC technology into aerospace and energy sectors for many years. We are excited to partner with Michigan and Wolfspeed to help elevate this technology to 150 mm with advanced packaging and integration,” remarked Matt Francis, CEO and founder of Ozark IC.
Researchers at Michigan Engineering will enhance and standardize a process development kit and transistor models. They intend to develop libraries of commonly-used circuit blocks to facilitate greater accessibility of SiC technology for integrated circuit designers.
“We will evaluate devices and circuits developed by NASA and GE Aerospace and packaged by Ozark IC and collaborate to standardize those components,” Peterson noted. “Additionally, we will leverage the data to produce process development kits and open electronic design automation, or open EDA, software that can assist in automating integrated circuit design and performance modeling. Our goal is to create sophisticated refined models so that future users have all the necessary tools to design and manufacture commercial products using this innovative technology.”
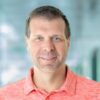
To achieve this, a group spearheaded by David Wentzloff, a professor of electrical and computer engineering at U-M, will enhance the distinctive open-source resources they have created for designing analog and mixed-signal circuits. These circuits are essential for functions such as power management, transforming real-world data from sensors into digital information for processing, and operating actuators and controllers within jet engines. Analog circuits serve to complement the digital ones that handle processing and memory tasks, for instance. While open-source design resources for digital circuits are becoming more prevalent, U-M is integrating them into the analog domain to facilitate the implementation of both analog and digital systems on a SiC chip.
“Our approach stands apart from previous analog circuit design automation tools,” Wentzloff remarked. “The key distinction is that we build upon highly developed digital design automation tools—in essence, analog circuits designed with digital design automation resources. This accelerates the design process for analog and mixed-signal circuits and makes it more attainable for a broader spectrum of designers. Specialized analog circuit design expertise is no longer necessary.”
Enhancing aerospace engine reliability
The silicon-based electronics currently utilized in engine control systems are restricted to a maximum of 257 F (125 C) and must be shielded from high temperatures through intricate and heavy cooling systems or by being placed in cooler sections of the engine. SiC electronics, however, can operate effectively in high-heat areas within engines and their exhaust systems. The innovations introduced in this initiative will facilitate new functionalities for sensors and actuators, adaptable modular control systems, reduced weight, and more straightforward engine electrical system architectures. Given SiC’s capability to endure extreme temperatures, SiC electronics could also propel the development of emerging hypersonic aircraft systems that function at temperatures significantly exceeding those manageable by silicon.
The initiative is titled: “Enhancing Engine Reliability and SWAP with 350-500 C SiC Electronic Systems.” It is one of 34 technical projects funded in 2024 by the U.S. Department of Defense under the Microelectronics Commons program, a program initiated by the CHIPS Act to boost U.S. leadership in microelectronics.
The University of Michigan is a founding participant in the Silicon Crossroads Microelectronics Commons Hub, which is directed by the Applied Research Institute. The SCMC Hub represents an innovation ecosystem with diverse collaborators dedicated to accelerating the growth of America’s microelectronics foundation by utilizing robust collaborative practices that strategically promote innovation, workforce development, and infrastructure requirements to achieve excellence in domestic microelectronics.