“`html
A spherical model that can alter its exterior from sleek to pockmarked minimizes drag and generates lift
Underwater or aerial crafts with dimples akin to golf balls could exhibit improved efficiency and control, a recent prototype from the University of Michigan has shown.
Golf ball dimples reduce pressure drag—the resistance an object faces when traversing a fluid—allowing the ball to travel 30% further than an unblemished ball on average. Motivated by this, a team of researchers crafted a spherical prototype with customizable surface dimples and assessed its aerodynamics in a controlled wind tunnel environment.
“A dynamically adaptable outer layer on an underwater vehicle could significantly decrease drag while negating the necessity for projecting appendages like fins or rudders for navigation. By actively modifying its surface texture, the craft could attain precise maneuverability alongside improved efficiency and command,” stated Anchal Sareen, U-M assistant professor of naval architecture, marine engineering, and mechanical engineering and lead author of two studies published in Flow and The Physics of Fluids.
These agile vehicles could reach typically challenging zones in the ocean while conducting monitoring, charting unexplored territories, or gathering data on water conditions.
Sareen and colleagues constructed the prototype by stretching a thin layer of latex over a hollow sphere speckled with holes, resembling a pickleball. A vacuum pump lowers the pressure in the core, drawing the latex inward to form precise dimples when activated. Deactivating the pump renders the sphere smooth once more.
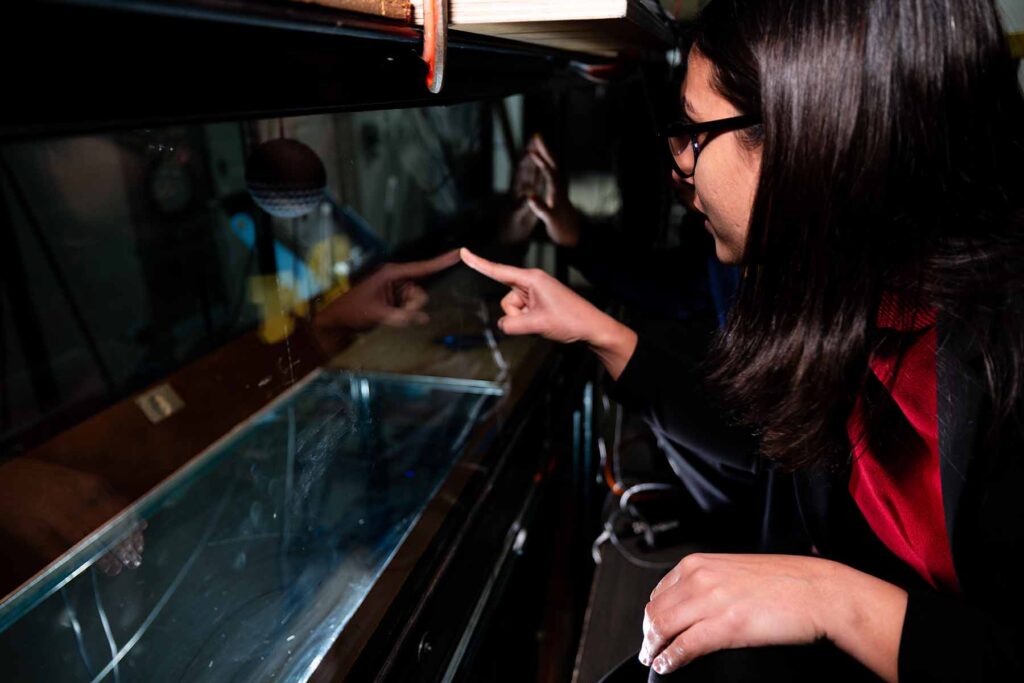
To examine how the dimples influenced drag, the sphere was subjected to tests in a 3-meter-long wind tunnel, held by a slender rod and exposed to varying wind speeds.
For each flow condition, dimple depth could be meticulously modified by adjusting the vacuum pump’s strength. Drag was quantified using a load cell, a sensor that measures the force exerted by airflow on the object. Simultaneously, an aerosol was sprayed into the wind tunnel while a high-speed laser and camera monitored the movement of the minuscule particles as they flowed around the sphere.
At higher wind speeds, shallower dimples effectively reduced drag while deeper dimples proved more efficient at reduced wind speeds. By varying dimple depth, the sphere achieved a 50% drag reduction compared to a smooth counterpart under all situations.
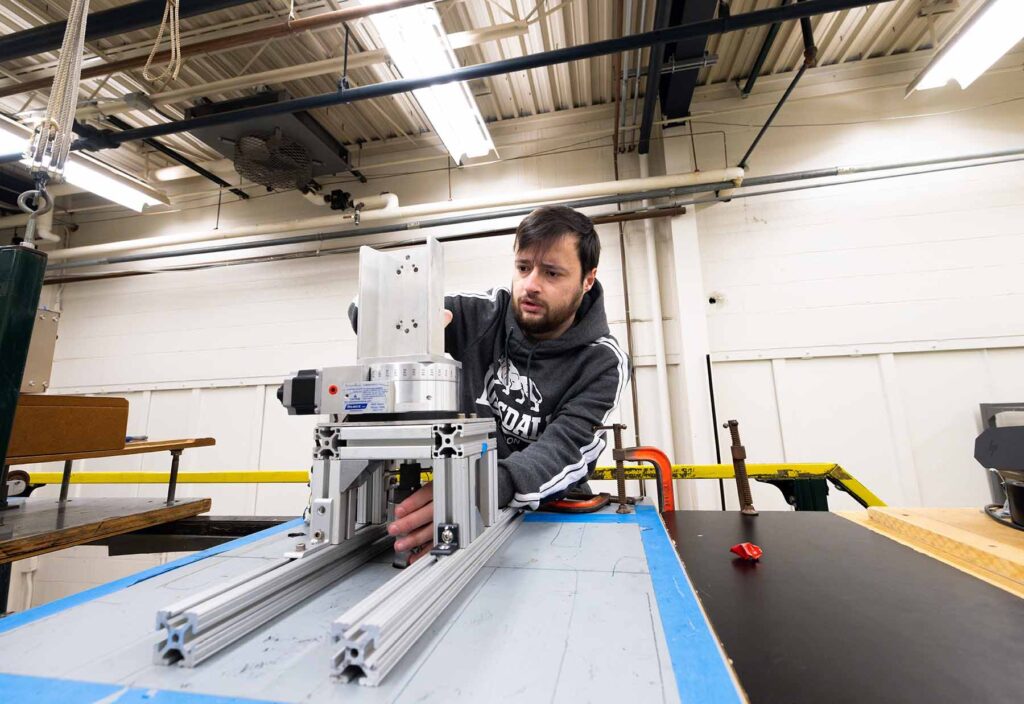
“The adaptable skin system can detect variations in the speed of incoming air and adjust dimples correspondingly to sustain drag reductions. Incorporating this idea into underwater vehicles would diminish both drag and fuel consumption,” remarked Rodrigo Vilumbrales-Garcia, a postdoctoral research associate in naval architecture and marine engineering at U-M and co-author of the studies.
The intelligent morphable sphere can also generate lift, facilitating controlled movement. Often recognized as the upward force that keeps aircraft aloft, lift can act in any direction as long as it remains perpendicular to the flow’s direction.
To achieve this, researchers structured the inner skeleton with openings on merely one side, causing the sphere to manifest one smooth and one pockmarked side upon activation.
This created asymmetric flow separation across the two sides of the sphere, redirecting the wake toward the smooth side. According to Newton’s third law, the fluid exerts an equal and opposite force toward the rough side, effectively propelling the sphere in the direction of the dimples. Dimples on the right generate force to the right while those on the left push left. This facilitates precise navigation by selectively activating dimples on the chosen side.
The team evaluated the new sphere in the identical wind tunnel setup with differing wind velocities and dimple depths. With the optimal dimple depth, the partially rough/partially smooth sphere produced lift forces up to 80% of the drag force. The lift generated was as powerful as the Magnus effect, but rather than relying on rotation, it was entirely created by altering the surface texture.
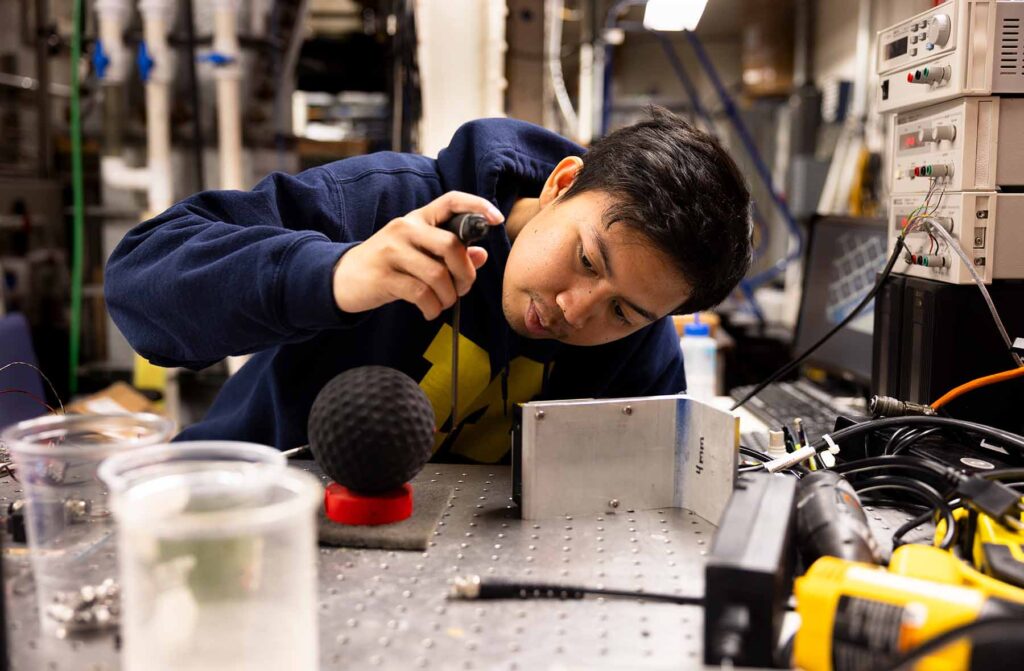
“I was intrigued that such a straightforward method could yield results comparable to the Magnus effect, which necessitates continuous rotation,” stated Putu Brahmanda Sudarsana, U-M graduate student in mechanical engineering and co-author of the studies.
“In the long term, this could be advantageous, for instance, for compact spherical robotic submarines prioritizing maneuverability over speed for exploration and inspection. Typically, these submarines would require numerous propulsion systems, but this mechanism could help minimize that need.”
Looking forward, Sareen envisions partnerships that merge expertise in materials science and soft robotics, further enhancing the capabilities of this dynamic skin technology.
“This intelligent dynamic skin technology could revolutionize unmanned aerial and underwater vehicles, presenting a lightweight, energy-efficient, and highly responsive alternative to conventional jointed control surfaces,” she remarked. “By allowing real-time adjustments to changing flow conditions, this innovation holds the promise of improving maneuverability, optimizing performance, and unlocking new design possibilities for vehicles.”
“`