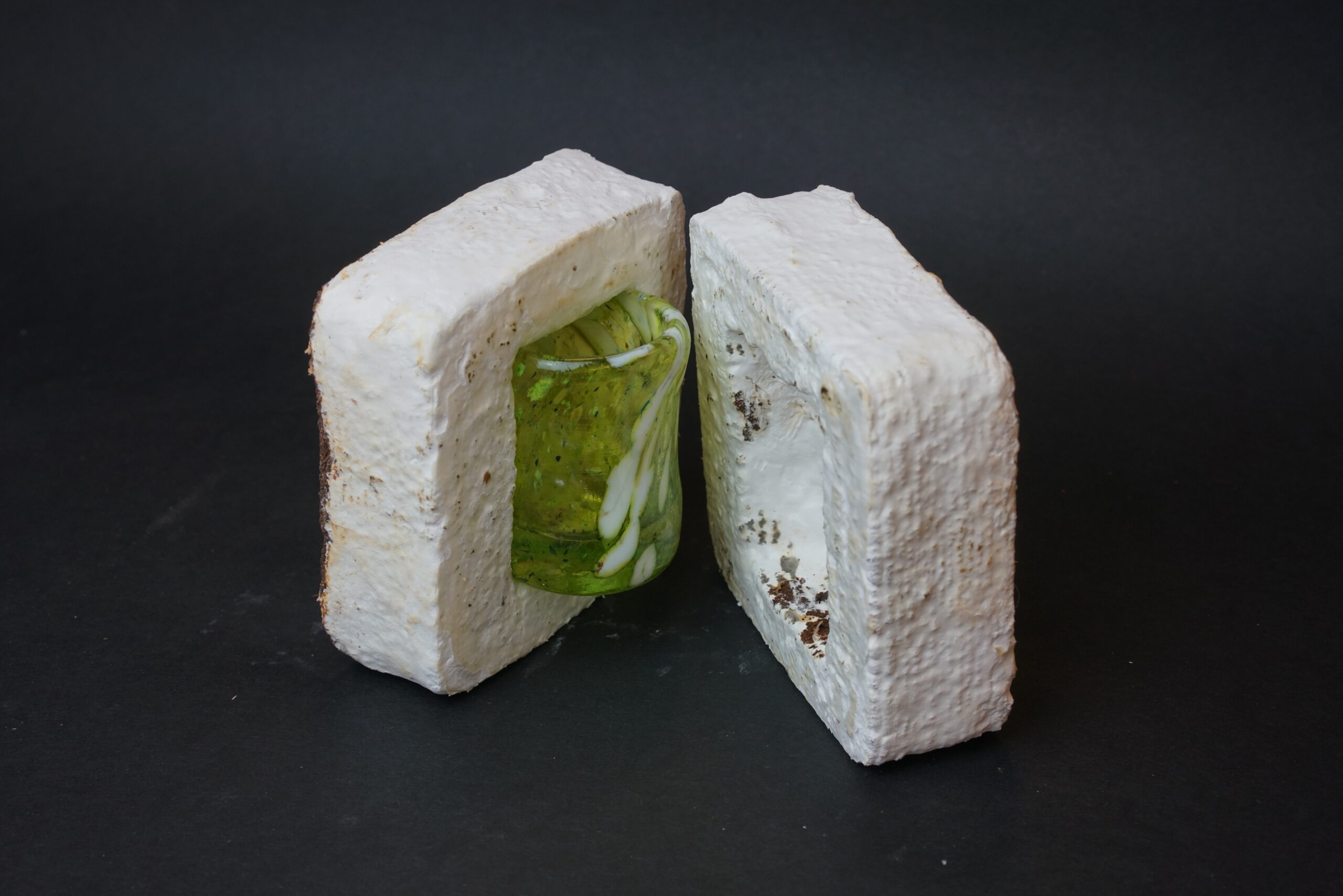
The cushioning material surrounding this petite glass was constructed via 3D printing using recycled coffee grounds. An exterior layer of white mycelium (akin to a fungal root network) envelops it, transforming the grounds into a biodegradable substitute for Styrofoam.Luo et al./3D Printing and Additive Manufacturing
Only 30% of a coffee bean dissolves in water, and many brewing techniques aim to extract even less than that. Hence, out of the 1.6 billion pounds of coffee consumed by Americans annually, over 1.1 billion pounds of grounds end up discarded from filters into compost bins and trash receptacles.
While observing the accumulation of grounds from her espresso machine, Danli Luo, a doctoral candidate at the University of Washington specializing in human-centered design and engineering, identified a potential. Coffee is rich in nutrients and is sterilized during brewing, making it suitable for cultivating fungi, which initially generates a “mycelial skin” before developing into mushrooms. This skin, resembling a white root structure, can connect loose materials and form a strong, lightweight, and water-resistant substance.
Luo and a team from UW devised an innovative method to convert those coffee grounds into a paste, utilized for 3D printing various items: packaging materials, elements of a vase, and a small figurine. They inoculate the paste with Reishi mushroom spores, prompting the growth of mycelial skin on the printed objects. This skin transforms the coffee grounds—regardless of their intricate shapes—into a durable, entirely compostable alternative to plastics. For detailed designs, the mycelium bonds individually printed segments to create a unified object.
The team published their research on January 23 in the journal 3D Printing and Additive Manufacturing.

Moving from the top left to the bottom right: the 3D printer constructs a design; three sections of a vase; the vase parts are assembled while still partially set; mycelium develops on the coffee paste; the vase integrates into a single piece; the completed vase accommodates flowers and water.Luo et al./3D Printing and Additive Manufacturing
“We’re particularly focused on establishing systems that can assist individuals such as small business proprietors creating low-volume products—like fragile glassware that requires sturdy packing for transport,” remarked lead author Luo. “Thus, we’ve been experimenting with novel material formulations to replace options like Styrofoam with something more eco-friendly and easily adaptable for small-scale manufacturing.”
To formulate the “Mycofluid” paste, Luo combined used coffee grounds with brown rice flour, Reishi mushroom spores, xanthan gum (a prevalent food thickener found in ice creams and salad dressings), and water. Furthermore, Luo engineered a new 3D printer nozzle for the Jubilee 3D printer designed by UW’s Machine Agency lab. This upgraded printing system can accommodate up to a liter of paste.
The team printed a variety of items using the Mycofluid: packaging for a small glass, three segments of a vase, two halves of a Moai statue, and a two-piece coffin the size of a butterfly. The items were then allowed to sit covered in a plastic container for 10 days, during which the mycelium developed a protective layer around the Mycofluid. In the cases of the statue and vase, the separate parts fused together.
This process mirrors that of homegrown mushroom kits: maintaining moisture for the mycelium as it thrives on nutrient-dense material. If left in the container for a longer duration, actual mushrooms would emerge from the items, but they are taken out once the white mycelial skin has formed. The researchers then air-dried the pieces for 24 hours, effectively halting the mushroom fruiting process.
The resulting material is heavier than Styrofoam, akin to the density of cardboard or charcoal. After an hour in water, it absorbed merely 7% more in weight and dried back to nearly its original weight while preserving its shape. Its strength and resilience matched those of polystyrene and expanded polystyrene foam, the material typically used to produce Styrofoam.
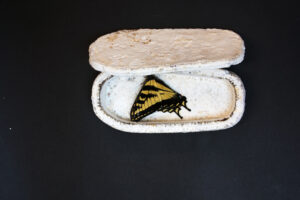
Utilizing 3D printing with coffee grounds enables the fabrication of intricate, interlocking components — exemplified by this butterfly coffin.Luo et al./3D Printing and Additive Manufacturing
Although the research team did not conduct specific tests on the material’s compostability, all of its constituents are compostable (and, in fact, edible, though not particularly palatable).
Due to the requirement for relatively uniform used coffee grounds, scaling up production with Mycofluid would present challenges, yet the researchers are keen on exploring other recycled materials that may yield comparable biopastes.
“We are enthusiastic about broadening this to include other bio-derived substances, such as various types of food waste,” noted Luo. “We aim to support a diverse range of flexible development, not merely to present a singular solution to the significant issue of plastic waste.”
Junchao Yang, a UW master’s student in human-centered design and engineering during this study, serves as a co-author, while Nadya Peek, a UW associate professor of human-centered design and engineering, is the principal author. This research received funding from the National Science Foundation.
For more details, reach out to Luo at [email protected].