A stabilizing layer on an electrode, integrated with microscale channels, assists in resolving the conflict between range and charging speed, even in frigid conditions
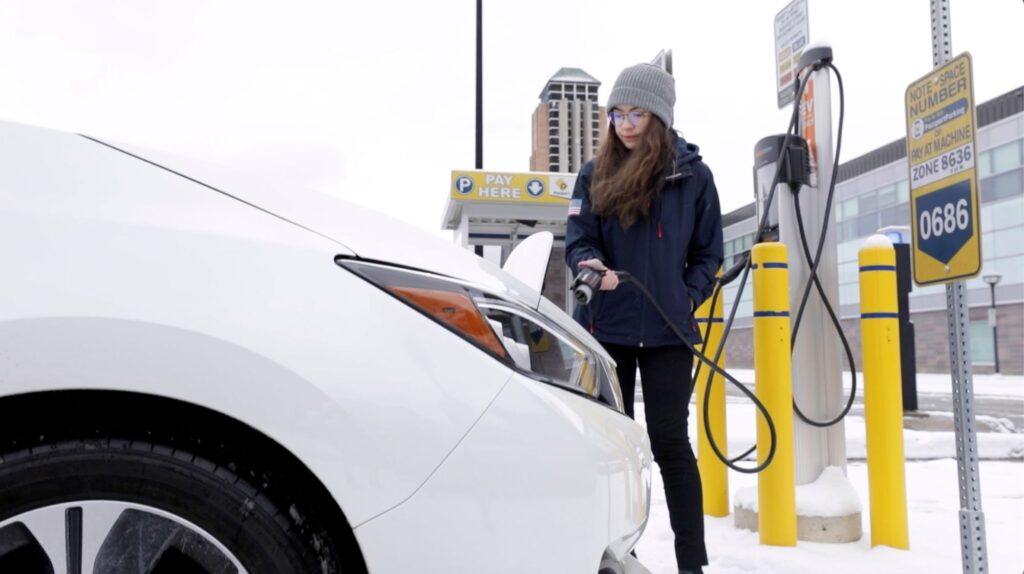
A revamped production method for electric vehicle batteries, created by engineers from the University of Michigan, may provide extended ranges and rapid charging capabilities in colder climates, addressing issues that deter potential EV purchasers.
“We foresee this method as one that manufacturers of EV batteries could implement without significant modifications to their current facilities,” commented Neil Dasgupta, associate professor of mechanical engineering and materials science at U-M, and principal author of the study published in Joule.
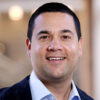
“For the first time, we’ve demonstrated a method to achieve extremely rapid charging at low temperatures, without compromising the energy density of the lithium-ion battery.”
Lithium-ion EV batteries produced in this manner can charge 500% faster at temperatures as low as 14 F (-10 C). The design and coating developed by the research team inhibited the formation of performance-limiting lithium plating on the electrodes. Consequently, batteries with these enhancements retain 97% of their capacity even after undergoing rapid charging 100 times in very low temperatures.
Present-day EV batteries store and discharge energy through the oscillation of lithium ions between electrodes via a liquid electrolyte. In lower temperatures, this ion movement becomes sluggish, hindering both battery performance and the charging rate.
To boost range, automakers have increased the thickness of the electrodes within battery cells. While this has allowed them to guarantee longer journeys between charges, it complicates some lithium access, causing slower charging times and diminished power for a given battery mass.
Previously, Dasgupta’s team enhanced battery charging performance by establishing pathways—approximately 40 microns in size—in the anode, which is the electrode that receives lithium ions during the charging process. By employing lasers to drill through the graphite, lithium ions were able to locate spots to lodge more quickly, even deep inside the electrode, ensuring a more even charging process.
This significantly expedited room-temperature charging; however, cold charging remained inefficient. The researchers pinpointed the issue: the chemical layer that develops on the electrode surface due to reactions with the electrolyte. Dasgupta likens this behavior to butter: a knife can penetrate it whether warm or cold, but it’s much more difficult when cold. Attempting to charge rapidly through that layer causes lithium metal to accumulate on the anode, similar to a traffic jam.
“That plating hinders the entire electrode from being charged, further diminishing the battery’s energy capacity,” explained Manoj Jangid, a senior research fellow in mechanical engineering at U-M and study co-author.
The team aimed to inhibit the formation of that surface layer. They achieved this by covering the battery with a glassy substance composed of lithium borate-carbonate, roughly 20 nanometers in thickness. This coating significantly improved cold charging speeds, and when combined with the channels, the team’s test cells charged at a rate 500% faster in sub-freezing conditions.
“By leveraging the synergy between the three-dimensional structures and artificial interface, this research simultaneously tackles the challenge of rapid charging at low temperatures while ensuring long-range driving capability,” remarked Tae Cho, a recent Ph.D. graduate in mechanical engineering and the study’s lead author.
In the last twenty years, EVs have grown increasingly common on the roads as consumers seek better environmental solutions. Yet, AAA survey findings indicate that sustaining this momentum is challenging. From 2023 to 2024, the percentage of U.S. adults who reported they would be “likely” or “very likely” to purchase a new or used EV fell from 23% to 18%.
Additionally, 63% expressed they would be “unlikely” or “very unlikely” to select an EV as their next vehicle purchase. Concerns surrounding reduced range in winter, coupled with slower charging, were widely highlighted during the January 2024 cold snap.
“Charging an EV battery demands 30 to 40 minutes even for advanced fast charging, and that duration extends to over an hour during the winter. This is the challenge we aim to overcome,” Dasgupta stated.
Subsequent efforts to establish factory-adaptable processes receive funding from the Michigan Economic Development Corporation through the Michigan Translational Research and Commercialization (MTRAC) Advanced Transportation Innovation Hub.
The devices were created in the U-M Battery Lab and analyzed at the Michigan Center for Materials Characterization.
The team has sought patent protection with assistance from U-M Innovation Partnerships. Arbor Battery Innovations has acquired a license and is working to bring the channel technology to market. Dasgupta and the University of Michigan have a financial stake in Arbor Battery Innovations.